Roofers are trained professionals who can safely and efficiently install a new or replacement roof. It’s a labor-intensive job that requires specialized knowledge of safety protocols and handling heavy materials at high heights.
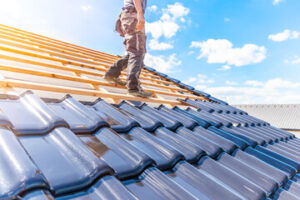
Before putting down the shingles, contractors lay down protective tarps and remove any existing shingles. They also set up metal flashing around chimneys, skylights and joints, and along the ridge of the roof to keep water out at those vulnerable spots.
A roof installation is a meticulous process that involves removing the old roofing materials, inspecting the underlying deck, making any necessary repairs, and installing underlayment, insulation, new gutters and drains, and a new roof. To ensure the success of this project, a homeowner can prepare their property by taking the following steps.
If you have a garden or flower beds near your house, cover them with tarps to prevent them from getting damaged by falling debris and nails. Also, move outdoor furniture and grills to a different area of the yard so that they are not in the way of the roofing crew. If you have children or pets, keep them away from the construction site. Metal flashing and shingles can scratch and bite, and the noise from hammers and nails striking the roof can be unsettling for them.
Before the roofer begins putting on the shingles, they will install underlayment and sheathing to protect the roof deck from moisture and ice damage. Underlayment consists of sheets of plywood, fiberglass mats or felt that are installed over the sheathing. The sheathing is then covered with an adhesive starter strip, which helps to keep the underlayment in place and creates a water barrier to prevent leaks.
Then, the shingles are put down in rows, starting with the bottom row. Each shingle is secured with a nail that overlaps the one next to it and is then nailed down firmly. The roofer will also install sheathing around the chimney, wood stove pipes, vents and certain valleys to prevent moisture buildup in these areas. They will also add ridge vents to provide air flow in the attic and maintain proper temperature balance.
During the roofing process, vibrations will cause dust to fall through light fixtures and other ceiling penetrations. A good idea is to take down wall-hung pictures and other decorative items, as well as cover or move fragile mementos and knickknacks to a safer location in the house that will not be affected by vibration. You should also plan on moving any children’s toys, patio furniture and other outdoor items to a safe place in the yard for the duration of the roofing project.
Materials
The type of roofing materials you choose for your home will affect its appearance and price. Among the most popular types of roofing materials are wood shingles and shakes, asphalt shingles, clay tiles and concrete tiles. Other roofing materials include solar shingles, which convert sunlight into electricity and are used on sloped roofs; membrane roofing (typically a single-membrane system like EPDM or rubber) for low-slope roofs; and metal roofing.
Shingles and shakes are crafted from natural wood, most commonly pine, cedar or cypress. They come in different shapes, sizes and textures. Shingles are milled into uniform length, width and thickness to create a clean look; shakes are hand split into thick wedge-shaped slabs that add an attractive, rustic texture. Generally, shingle roofs are less expensive than shakes.
Tiles are often found on Spanish, Mediterranean and Southwestern-style homes. They are available in various shades and textures, making them a beautiful addition to any home. However, they can also be very expensive and require a bit more maintenance than other roofs.
Rolled roofing is one of the most affordable options and works best on low-slope roofs. It consists of long rolls of asphalt-impregnated material topped with mineral granules. These sheets are held together by hot-melted tar or cold-applied adhesive. It’s not a good choice for flat roofs, though, and tends to have a short lifespan of about five to ten years.
Another economical option for low-slope roofs is membrane roofing. It’s typically a single-membrane system made from Neoprene, PVC or the ever-popular rubber EPDM. These roofs are watertight and withstand extreme temperatures, but they don’t protect against the sun’s UV rays.
Solar shingles are the latest in roofing technology and are designed to absorb and harness sunlight for energy. You’ll need a roofer who specializes in this specialty to install them, and they’re not cheap. But they can reduce your energy bill and increase the value of your home, so they can make an excellent investment. In some areas, solar shingles are a tax-deductible expense.
Installation
Roofing installation is a complex job that requires knowledge of proper safety protocols and the ability to handle materials at potentially high heights. It’s a task best left to professional roofing contractors who have the skills, equipment, and experience to complete the project safely and effectively.
During this phase, the contractor will remove any existing shingles and underlayment, if necessary. They will also install vents and roof pipes, if needed. Once they’ve confirmed that the underlayment is dry, they will begin installing new shingles. The shingle installers will start in the middle of your home, working their way towards the edges. This ensures that any leaks will begin in the middle of the roof and not at the edges, where they would be more difficult to detect.
The shingles will be installed in a staggered pattern, with close nails near the edge of each row and wider nails farther from the center. This will help prevent water from penetrating the shingles and causing damage to the underlayment and interior of your home. Kickout flashing will also be installed to prevent water from seeping between the wall and gutter.
Final Inspection
One of the most important things a contractor can do to prepare for final inspection is create a rapport with their inspector early in the project. This will allow them to discuss revisions and expectations along the way, rather than catching the inspector by surprise at the end. Having an established line of communication will also make it easier for the inspector to communicate any issues or concerns that they may have.
The inspector will look at a lot of different elements when doing the final inspection, so it’s important to understand what they’ll be checking for ahead of time. The pre-inspection and penultimate inspection will help to establish this, but it’s always a good idea to ask the inspector what they’re looking for on the day of the final inspection.
This will help to reduce the likelihood that something will be missed on the final inspection, especially if the issue is related to safety or egress. For example, if the building is lacking in a fire exit or handrail clearance, these issues would need to be addressed urgently in order to ensure that people can safely escape the space.
Other common issues can include a lack of signage, electrical issues, or improper framing. The inspector will assess how easily and affordably these can be fixed, as well as the impact on occupant safety, in order to decide whether to approve the final inspection.
A final inspection is the last step before a construction site can be closed off and made ready for occupancy. The process involves the approved agency inspecting all parts of a structure to verify that it has reached the point of final completion. This includes ensuring that all aspects of the construction are in accordance with the original approved building plans. The agency will also report any issues with the work to the contractor.
If the final inspection is satisfactory, the approved agency will issue a letter of completion or certificate of occupancy to the owner. It is important to keep in mind that if the inspector finds any issues with a construction project, it could result in the need for further evaluation or even termination of the contract. Therefore, the best way to avoid a failed final inspection is to document everything and create organizational systems. This will not only reduce the chances of a failure but it will also help to streamline the final inspection process.